Written for the IDA Detail Dialogue, Published December 2022
In detailing, we naturally obsess over tiny details – hence the name, I suppose. A smudge, fingerprint, speck, or stain can and will spoil a detailer’s day since honing in on perfection is what drives us to achieve those ever-elusive ‘highest quality results.’ In our quest for reaching detailing nirvana, small points of difference become intensely magnified.
Machine polishing pads seem like simple products… It looks like you take an engineered foam – manufactured with various physical properties and characteristics – slice it into sheets, attach a loop backing, cut everything into round discs and there you have it. The thing is, there are a ridiculous number of variables in that process that all add points of difference, however small, to the end product.
Let’s compare Lake Country Manufacturing’s SDO and HDO pad ranges. Despite using the exact same foams for cutting and polishing, the design and construction of the HDO pad is intended for detailers with higher demands, working faster and harder, so they have a higher performance envelope than their more basic SDO brethren.
How and why can this be?
Good question. A lot comes down to the dense sandwich layer, sitting beneath the main cutting/polishing foam, which itself is thinner than on the SDO.
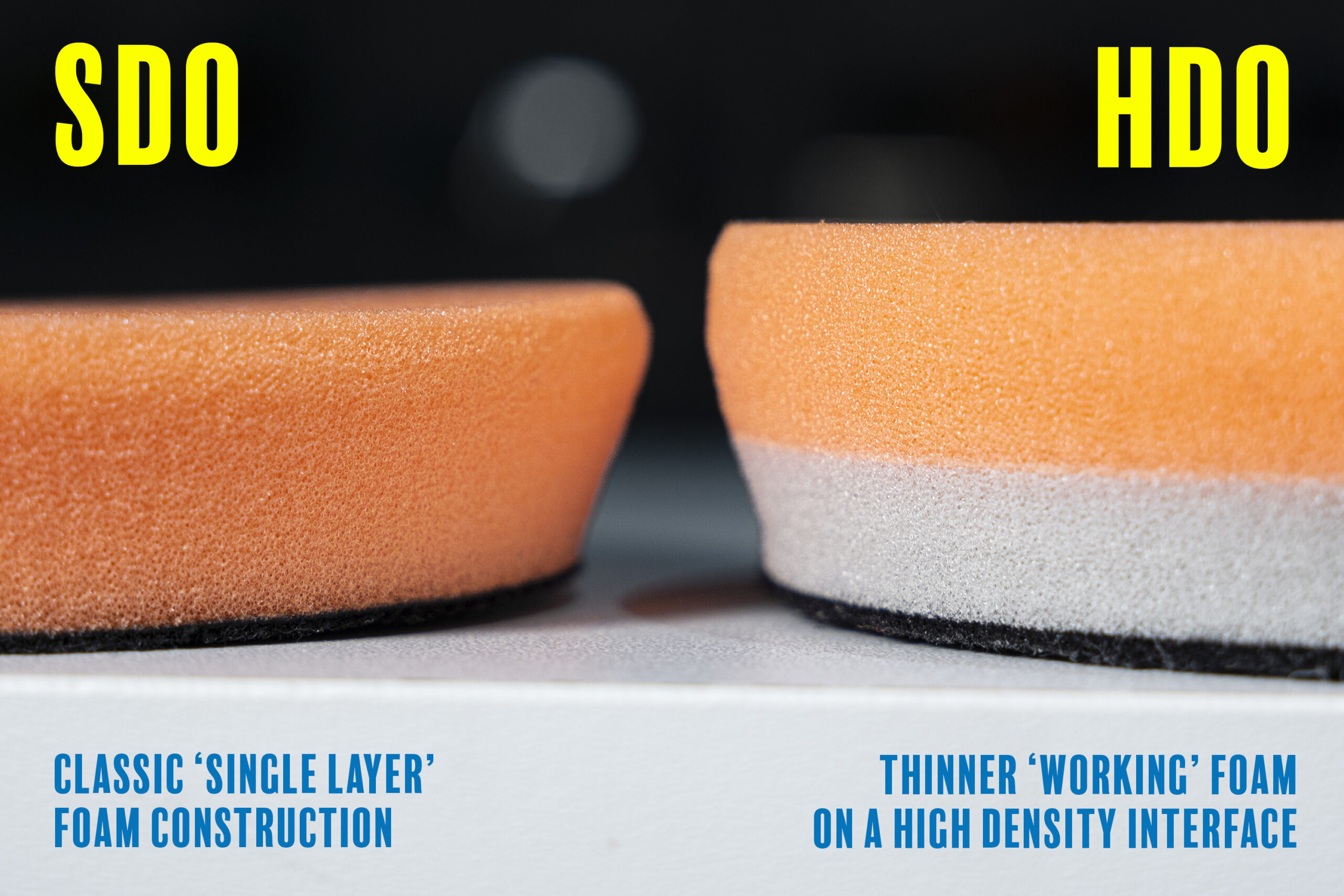
Why?
Larger-throw orbital polishers have become popular thanks to their extra cutting prowess (and associated efficiency gains). Larger throw = more movement = more work done. But foams are squishy to at least some degree, and we identified that traditional single-layer foam pads can flex internally under all that aggressive to-ing and fro-ing, with the friction at the pad face acting as a kind of brake. If the foam absorbs some of the action, the polisher is trying to provide 15 or 21mm orbital movements, but the cutting/polishing face could be doing 11 or 15mm movements instead. And less movement = less work done.
Thanks to the very firm interface layer and the thinner ‘active’ foam, HDO pads minimize this effect. On long-throw orbital polishers, they cut and polish noticeably more effective than traditional pads as a direct result.
Coming back full circle – this is how what may seem like a minor point of difference can make a large difference overall. In the case of HDO pads, that could require shorter or fewer passes to achieve your correction goals, saving time, increasing efficiency, and perhaps ultimately helping to make more money.
The firm backing is just one point of difference, though. I’ve received so much feedback praising Lake Country pads for their durability, and that’s not happened by accident; it’s about the quality of the foam materials, the loop, the adhesives and so on. There can be a surprising difference between two very similar looking / feeling foams or fibers. Trust me, I’ve tested hundreds.
Within our HDO line, we also have a couple of microfiber options, differentiated from the standard versions by a center hole and tapered edge. That’s right – we cut out a center hole and bevel the edge of the pad, but otherwise, our HDO microfiber pads are the same materials as the standard ones…see a pattern?
Again, these small points of difference earmark the pads for Heavy Duty Orbital work using a larger-throw orbital polisher. The center hole promotes better pad cooling, which is necessary since there’s more movement/work going on and hence a greater potential to heat build-up. The tapered edge not only allows for better access in tighter areas but also makes a big difference when you start using more advanced pad-tilting techniques, which offer cut and efficiency gains (plus improved cooling, but that’s for another article). The extra material tapering out beneath the backing plate edge means you’ll maintain optimal contact between the fibers and paint surface if you tilt to a slight angle (like Kelly Harris and I do).
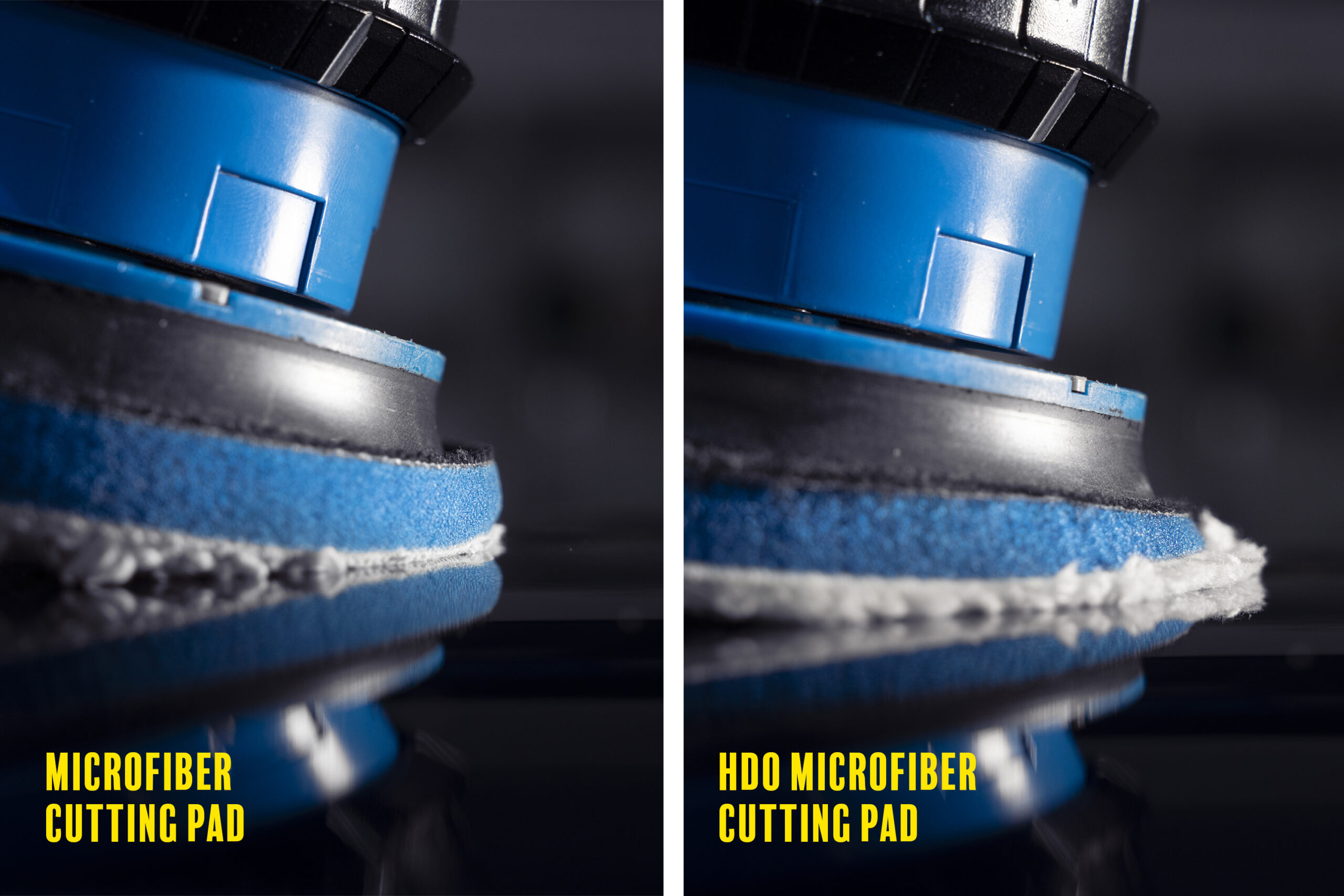
Conclusion
Let’s return to the titular question of this article, which I’ve actually been answering all along. You’d need an HDO pad because you care about efficiency; because you’re interested in getting great results without so much effort; because you want to maximize the potential of your long-throw orbital polisher, and you want to do it with durable, reliable pads that have been designed from the ground up to withstand those demands, time and time again.
HDO pads cover the full spectrum of modern detailer’s needs – from the heavy cutting microfiber to the delicate black finishing foam – and are available in a range of sizes from 3” to 6”. You can also opt for our CCS technology on the foam variants for an extra ‘point of difference’ (I’ll summarize – they hold more compound and allow longer working times – I’ll do a full blog on this shortly).
Please contact me if you have any questions about this article or Lake Country products!
Until next time,
Jay @ LC
IG: /jaybroomdetailing
FB: /jay.broom.detailing
FB group: Detailing with Lake Country