What is Machine Polishing?
Using a machine polisher to polish paint is much more effective and efficient than polishing by hand, in the same way that tightening a screw is much faster with a power tool than a screwdriver. When we are ‘machine polishing’ paint, we are using ‘abrasion’ (the wearing away of the flawed paint surface material) to create a surface that is free from defects again (as we achieve ‘correction’).
Why Would You Machine Polish a Car?
A variety of surface defects can make vehicle paint look untidy, lifeless, unloved and dull. Some waxes, sealants and glazes applied on top of the paint can temporarily improve the look (like make-up), but they will wear down and wash away quickly. Machine polishing dramatically restores a vibrant gloss to the paint surface itself, enhancing the ‘true’ appearance of the car. With good aftercare and maintenance, the results will last for many years.
However, paint is a finite resource on a car’s surface. Typical ‘swirl marks’ are only around 1 or 2 microns deep, and typical clear-coat is about 40 to 50 microns thick, but the goal is always to remove just enough of the paint surface to deal with the apparent defects to a satisfactory degree – sometimes ‘improvement’ is the specified target, others it may be ‘absolute perfection’ – without over-shooting the target and sacrificing more paint than necessary.
For context, in case you’re wondering, a US dollar bill is around 75 microns thick…
What is a Buffing Pad/Polishing Pad?
Buffing pads and polishing pads are key components of the machine polishing process; the tool provides the movement, but buffing pads or polishing pads (attached to the tool) act as the polishing interface. Typical pads are circular in shape, but they can come in various sizes, thicknesses, densities, and materials to suit a range of applications. The three most common materials used are foam, wool and microfiber, although other materials such as synthetic blends, silk and denim can be found.
How Do You Attach a pad to a Machine Polisher?
Nowadays, most machine polishers are designed to be used with a backing plate—a cushioned rubber or plastic disk, screwed or bolted to the machine which spins / orbits (more on that later) with the mechanism inside.
Most polishing pads are attached to the backing plate via a simple hook and loop connection (often referred to as Velcro, although that is a brand name). Buffing pads are made with the fuzzy ‘loop’ material on the back, and machine polisher backing plates feature the grippy side (the ‘hook’) ready for the pad. When attaching the buffing pad to the backing plate, it needs to be centrally aligned, and the pad you’re using must be at least the same diameter as the backing plate (if not slightly larger) for optimal and safe operation.
Some classic styles of buffing pads (predominantly heavy cut wool pads) still feature a direct bolt-on design, and historical buffing bonnets were attached like a shower cap – though this is no longer popular!
How Do Polishing Pads Work?
Polishing pads transfer the rapid mechanical action from the machine polisher to the painted surface, which is why their design, construction, coarseness and other characteristics dramatically affect many aspects of the polishing process. The pad also acts as the carrier for liquid abrasives (compound and polish), which we use in combination with the pad; those liquids act as a lubricant, a coolant, and have abrasive characteristics of their own. The buffing pad, combined with the liquid compound or polish on its surface, creates a controlled and efficient polishing interface which we use to mechanically rub the paint surface and, through abrasion, wear it down.
What Makes Polishing Pads Different?
Because of the material and design differences between them, buffing and polishing pads can be more or less abrasive: we sometimes refer to how abrasive they are as to how much ‘cut’ they have or how ‘aggressive’ they are. Firm, rough, coarse pads will have more cut / be more aggressive than soft, fine, plush ones.
Materials, sizes, construction, coarseness, firmness, flexibility, all of these factors and more can make one pad work very differently from another, but each variable, even on its own, can have a noticeable impact. Take one example: two pads made from the same foam, identical in every way except how thick they are, will perform differently from one another under repeatable test conditions. This particular example is what led to the creation of the Lake Country Manufacturing HDO and SDO pad range, which we’ve explained the science behind on our YouTube channel.
Why Do I Need a Range of Pads?
When buffing or polishing a car, having a range of pads aids efficiency. You need the heavier cutting pads to remove surface defects reasonably quickly, and then the baton is handed to a less aggressive pad to remove any fine haze left by the previous stage(s). We use heavier cutting, more aggressive pads to deal with deeper defects and harder (denser) paint surfaces. Softer, gentler finishing pads are needed when the paint is softer (less dense) and require extra finessing to restore a perfect luster. This is why detailers carry out ‘stages’ or ‘steps’ using buffing pads that suit the task at hand.
Technically all polishing stages are abrasive, so even the finest of the fine leaves behind microscopic marring from that abrasion. However, by working cleanly with good quality pads and equipment, we can reach a point where the human eye detects pure gloss.
We know that we can find a variation in the hardness of paint from car to car (sometimes panel to panel), and there can be defects of different depths to contend with. In addition, vehicles come in all kinds of shapes and sizes (some with tricky-to-access areas) and there are multiple styles and sizes of machine polisher tools available too. Hence, buffing and polishing pad designs vary to suit specific purposes, and in order to work most efficiently and safely, it helps to have the right pad available for each scenario we encounter.
What Types of Polishing Pads Are There?
Although technically all buffing and polishing pads exist somewhere along an aggression spectrum, broadly speaking, there are three main types of pads: pads for heavy cutting, pads for gentle polishing (sometimes called ‘finishing’ or ‘jewelling’ pads), and pads for anywhere in between! More aggressive / heavier cutting pads typically remove paint material more quickly but tend to induce fine imperfections of their own. Soft, plush finishing pads remove very little paint material but can create the glossiest, shiniest results on the paint surface. Pads that fall in between will have ‘in-between’ capabilities.
Buffing and polishing pads are often made in a particular design and then offered with a range of cut options within that design. For example, the Lake Country Manufacturing SDO foam pad range comes with three cut-level options (blue foam for heavier cutting, orange foam for medium-to-light polishing, and black foam for final finishing). All three pads are identically constructed (the same size, shape, taper), but the different foams mean each has a very different amount of cut that makes them suitable for different stages of the polishing process.
Furthermore, buffing and polishing pads range in size from 1” to 8” and above (you’ll want the big ones when polishing the side of a yacht and the small ones in the aero vents on a supercar). Some feature curved edges, some tapered, some are flat; some have textured polishing faces, others are smooth; some can be inches thick, and others barely 1/4 inch. The variety of pads allows for enormous specialization as well as catering to user preferences.
Which Buffing Pads Are Most Aggressive?
As a general rule of thumb: wool pads are more aggressive than microfiber pads, and microfiber pads are more aggressive than foam pads—this is due to the nature of the materials, but, that being said, there are overlaps. Some heavy-cutting microfiber pads will be more aggressive than the softest wool pads, and some softer microfiber pads will be less aggressive than the most aggressive foams.
Most automotive paint today (specifically the top layer, called ‘clear-coat’ or ‘lacquer’) is soft enough that very heavy cut pads are not often required. In previous decades, many manufacturers used tougher paint than is available now. This explains the trend away from wool pads towards microfiber for the initial defect removal/cutting stages, because nowadays a wool pad is more likely to be TOO aggressive for the task at hand.
What Are Wool Pads?
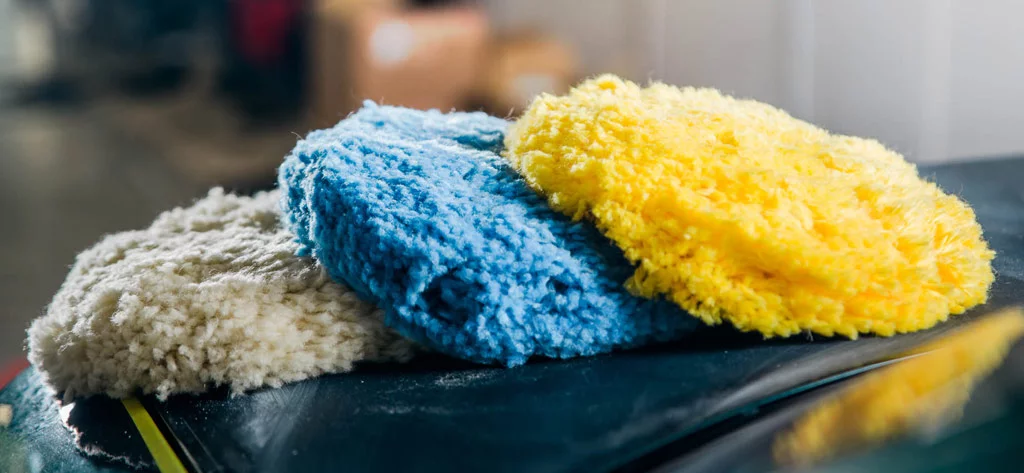
Wool pads are typically intended for heavy cutting purposes—made from either pure lambswool or a blend with synthetic or other natural fibers which can carry large quantities of cutting compound. Wool pads are detailing’s big hitters, capable of removing deep defects from tough paint with ease. Typical wool pads are knitted with 1” to 2” long strands, which can be twisted, straight, steamed, un-steamed, or any combination of the above to give heavy to extremely heavy cutting performance.
What Are Microfiber Pads?
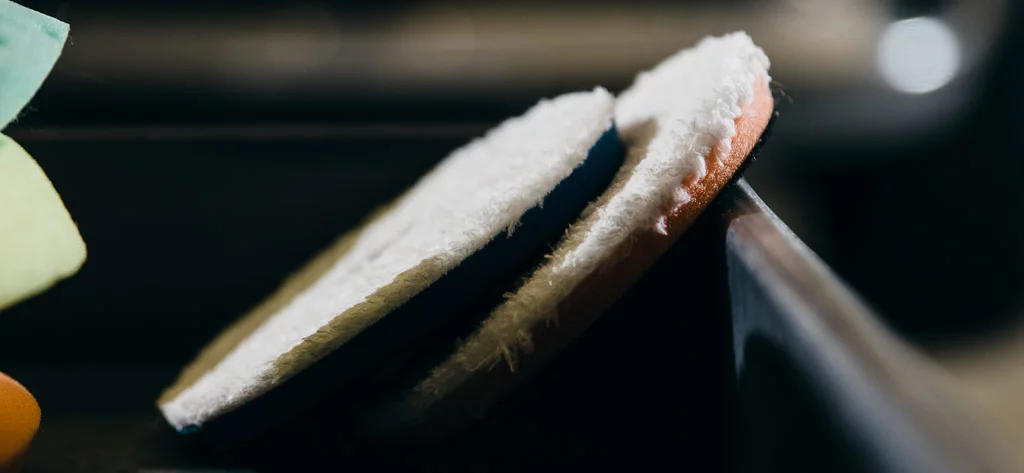
Introduced to the detailing industry in the early 2010s, microfiber cutting and polishing pads use modern technology to mate fine microfiber strands to a thin, controlled density foam backing. Both the fibers themselves (which can be shorter, longer, plusher or rougher) and the foam (which can be firmer, softer, thinner, thicker, tapered or straight-edged) affect the quality of results through variations in contouring, pressure application, feel, and outright abrasive performance. The combination of high surface area (thanks to the fiber pile) and inherent low-dust / clean operation qualities are why microfiber pads are gaining traction as the premier contemporary cutting stage pad choice.
What Are Foam Pads?
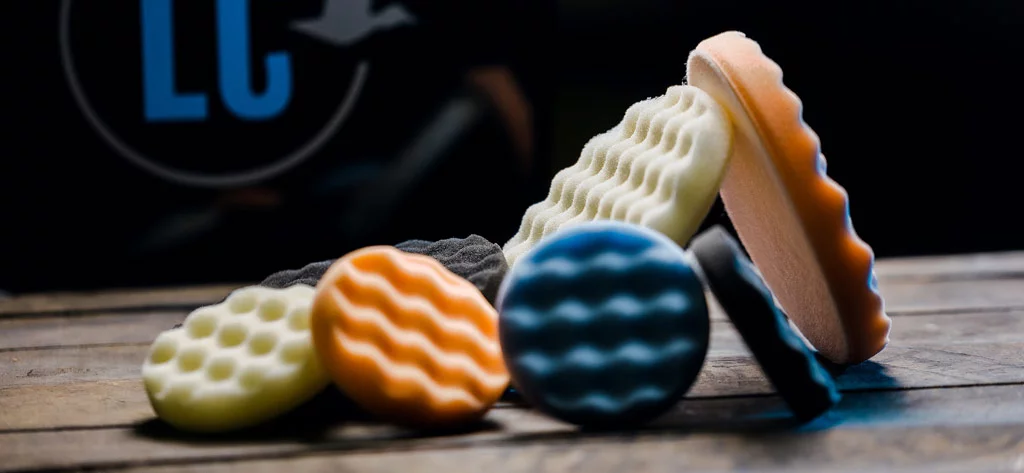
A staple pad material, foams have great cutting qualities and make arguably the most capable ‘one-step’ polishing pad, thanks to the even finish they leave behind. Medium cut foam pads can remove defects and finish with little detectable haze, saving detailers time with enhancement packages or when working on silver, white, or pale colored paints where the law of diminishing returns applies most. Softer foams, in particular, are the choice of most professionals when it comes to refined polishing / finishing / jewelling stages, where the cushioning from the foam itself, combined with the extremely even nature of its polishing face, combine to make it the ideal pad design for the ultimate finessed polishing action.
What Pads Work on a Rotary Polisher?
On a rotary polisher, the pad spins in a perfect circle; this means that with each revolution, the center of the pad barely travels at all (not doing a lot of work), but as you go further towards the edge, it travels much faster, doing more work. This is why rotary polishing, by its nature, offers the highest levels of aggression and so wool pads are a natural fit. The long strands on wool pads can carry a high quantity of compound, and as the pad rotates on the paint, they lay aligned, giving up that compound and using the length of their strands to cut the surface efficiently. Some wool pads are made with a short pile (like a microfiber), creating the exception to the rule, but in general, ‘normal’ wool pads are intended for rotary use. This video explains neatly why that is the case:
Foam pads are also a great fit for rotary work, especially at the polishing and finishing stages. Some foam pads have specialized designs to make them ‘rotary-specific,’ such as the Lake Country Precision Rotary and Curved Edge Rotary pads—which are made with a shape and contours that take into account the rotational action of the tool and the high-speed travel of the pad at its circumference.
What Pads Work With a DA/Orbital Polisher?
With any orbital polisher action (whether it be a Random Orbital polisher or a gear-driven / Forced Dual Action polisher), the pad is never truly ‘spinning’ like it would be on a rotary buffer, minimizing (basically eliminating) the risks associated with a high-speed pad edge. There’s much less of a difference in how much work the pad is doing between the center and the circumference—it’s a matter of a few %. Instead, the pad will be moving quite consistently in curly spiraled orbits across the entire face, effectively ‘oscillating’ at the edge.
Wool pads would be less effective on an orbital polisher with their long strands since the wool would flop around with the small orbital action, rather than transferring it through to the paint surface and abrading as intended. That’s why microfiber pads have a significant advantage—the short pile microfiber strands are designed to be the right length to work with that tighter pattern and effectively cut the paint surface while still carrying a high quantity of cutting compound thanks to their exceptional surface area.
Some microfiber pads, such as the Lake Country HDO-550F pad, are designed with specializations such as a tapered edge profile (which helps with cutting into tighter areas and gives additional protection from the backing plate) and a center hole – helping with ventilation and cooling in the middle where, on an orbital pad, it’s doing a lot of work and potentially creating the most heat.
One minor ‘drawback’ of microfiber pads is that it’s usually possible to see them leaving a faint haze behind, sometimes called ‘micromarring,’ after the cutting stage. Do not be alarmed! This is extremely fine and will be easily polished away by any final finishing pad.
Of course, foam pads are also a natural fit to any orbital machine polisher, and this combination remains one of the most popular worldwide. Foam polishing pads are available with an extensive range of cutting and polishing characteristics to suit almost all occasions. Today’s pads have been designed with contours, tapers and profiles that maximize the convenience, comfort and control available to the user. The Lake Country Manufacturing HDO pad design is an example of a unique specialization that takes things even further—an overall quite thick construction combined with a pronounced tapered edge. This is good for safety and access, but introducing a dense sandwich layer helps ensure the full movement of the backing plate is transferred to the paint surface, without the flexing losses that a thicker, more cushioned foam would experience. HDO foam polishing pads have quickly become a favorite among Heavy Duty Orbital polisher users (15mm and up), although they will work great on any orbital machine.
What Are Mini Polishing Pads and Micro Pads?
There is now a wide range of mini and micro polisher tools on the market, which often come with 3”, 2” and even 1” backing plates (which are often interchangeable). This means that detailers can physically access tighter and more intricate areas of a car than ever before, and polishing pads have been produced to suit! In the 3” range, almost anything you can get in standard larger sizes is available – same construction, same designs, same materials (you can even get 3” wool pads). At 2” and below, generally, microfiber and foam pads are all you need (and both will work in rotary or orbital modes at this size). Again, these can be found in a variety of cut levels and designs to suit detailers’ needs, such as 1” microfiber pads for removing heavy sanding marks in a hood vent or 2” medium cut foams for polishing a particular door jamb or sill plate. The possibilities are endless, but there’s a pad for every occasion!
How to Choose the Right Polishing Pad
Every detailer will eventually find their ‘go to’ pads which over time they have come to find the most comfortable to use, consistent and best performing, but here are two useful tips to remember if you’re just starting out:
- Don’t be a hero. If you don’t know how much material you’re removing or how much you need to remove, begin with a ‘middle of the road’ pad choice and test a small area of the vehicle to get a feel for how effective that pad choice was. Remember: the goal is to remove only just as much material as is necessary – if you remove too much, you might not realize you did.
- If you can catch your fingernail on a scratch, the likelihood is that scratch is not 100% rectifiable (without burning through the paint). See point above.
Don’t just think about the paint surface defects – does the pad fit? Consider the area and shape of the panel, adjoining panels and surfaces, gaps, and edges. Is a firm pad going to contour into a concave channel, or might it be smart to use a more pliable, flexible, maybe thicker pad? Is there a risk of knocking that wing mirror, which a different size pad would mitigate? Does your pad choice allow you to avoid excessively wearing away ridges, swage lines and other sensitive areas (check the video below for a great demo), or would a smaller pad make more sense? Can you prop open that door or hood for better access? A smart move is to take your pad in hand and just position it anywhere you aren’t certain of before going for it with the machine polisher.
Are Polishing Pads Reusable?
Absolutely. In use, polishing pads will gradually become saturated with spend compound/polish and paint residue, and by far, the best way to clean them out (whether they be wool, microfiber or foam) is with a dedicated pad washer. Lake Country released the System 4000 in 2021 and it has been an instant hit globally, for a good reason. This video demonstrates why it’s so important to clean your pads and how the System 4000 makes doing that so straightforward. With simple maintenance, your pads will be ready to polish time and time again:
However, other methods are available! You can clean them by hand with water and a mild detergent, which works well with foam pads. Wool pads and microfiber pads can benefit from being cleaned with a pad spur and/or blown out using compressed air, after which you can then use a washing machine on a gentle cycle with cool water once you’re done polishing. Always air dry any pad to prevent shrinkage of the loop backing or knitted fibers.
How Long Do Polishing Pads Last?
All good things must come to an end (even this FAQ blog, at some point…). Any polishing pad will eventually show signs of wear and tear with repeated use. This will happen quicker, in general, with cutting pads than with finishing pads, simply because of the heavier forces and abrasion involved. Running up against or over sharp badge corners, pushing super-hard, getting smoking hot, using needlessly high-speed settings – all of these will prematurely shorten a pad’s lifespan, as will expecting one pad to carry too much load. The smart thing to do is have several pads in circulation and switch between them, replacing only the ones that have reached the end gradually, rather than finding yourself over-reliant on a single pad which, if it fails, could leave you stranded.
All that being said: quality pads are designed to be used over and over again. It helps if they are taken care of and not pushed beyond their intended operation. Good quality cutting pads will easily be useful across multiple cars, and finishing pads will potentially last for dozens. But you’ll know it’s time to change when that cutting pad has gotten too matted, threadbare at the edge, clogs too easily, leaves behind too much haze, or when that finishing pad just won’t give you the ultimate gloss that it used to. That’s when you get to experience the singular joy of ‘new pad day.’
Detailers out there, you know I’m right 😉