Ah, the wool pad. Auto detailers, repairers, manufacturers, and refinishers around the world have loved, feared, and revered these natural buffing solutions since the dawn of the detailing industry itself. But now, with modern tools, techniques, and great advances in material technology, we ask the following question:
Is the classic wool buffing pad done?
A Brief Wool Introduction
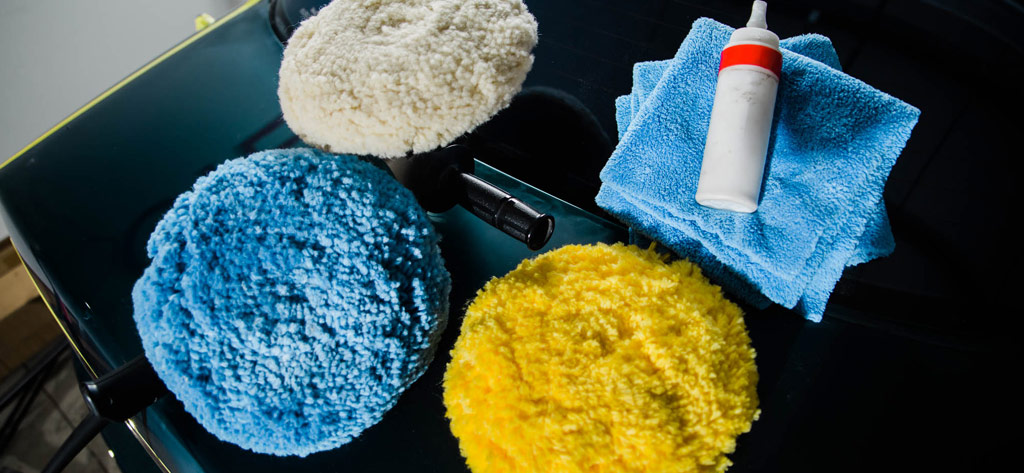
Wool buffing pads began as an inexpensive and durable buffing solution, while still having rather primitive qualities.
Modern detailers recoil in horror when they discover that initial designs of wool pads were attached directly to a rotary spindle by a bolt in the middle! The theory was that the wool pile would remain thick and plush enough that the fast-spinning metal bolt in the center wouldn’t come into contact with the painted surface.
Later designs took a more careful approach, where fully natural sheepskin and wool bonnets were fastened by a drawstring or elastic band onto a backing plate. Essentially, this design functioned like a sheepskin shower cap. This was still a very ‘rustic’ approach which relied on basic sheep leather materials, complete with all the inconsistencies you’d expect. Therefore, there remained many opportunities for improvement.
Over time, innovations such as hook and loop fastening, pre-twisting, steaming, tufting the wool, and others have helped to remove some of the quirks and irregularities from wool buffing pad designs. But from their inception through today, Lake Country is a world-leader in wool pad technology, manufacturing a super-reliable range of wool products that boast an increase in efficiency and durability. We’re proud that millions of our wool pads, especially our patented ‘Purple Foamed’ Wool Pads, are used worldwide.
The Issues With Wool
A look back in time highlights that wool was an early choice of buffing material. This is largely because of the natural characteristics of the fibers. Wool itself is not new technology; how humans have knitted and woven it for many purposes over the centuries is the real evolution in wool. This includes its uses in buffing and rubbing.
Specific to the context of car polishing, the fact that wool is made up of millions of abrasive strands, each with their own cutting ability, plus the capacity to carry a compound, is what makes wool a natural choice. But wool carries with it one major problem for automotive detailers: if anything, wool pads are a little too effective. Here’s how:
Early wool pads went hand in hand with traditional rotary polishers; there really was no significant alternative. What people found was that they got great cuts and could remove light, medium, and even heavy defects with incredible efficiency because of those abrasive fibers.
However, a side-effect of using a wool pad on a rotary polisher is that it’s really difficult to avoid leaving what we call ‘holograms’ behind. While rotating quickly, the wool fibers abrade the paint surface in concentric circles – that’s how correction works; the pad and compound wears the paint surface away until the defects are removed.
Unfortunately, holograms (also referred to by detailers as ‘buffer trails’) are an illusion made visible by a reflected light source bouncing off all those neatly aligned microscopic circular grooves at the same time, from the same direction. This effect can be similarly seen on a vinyl record.
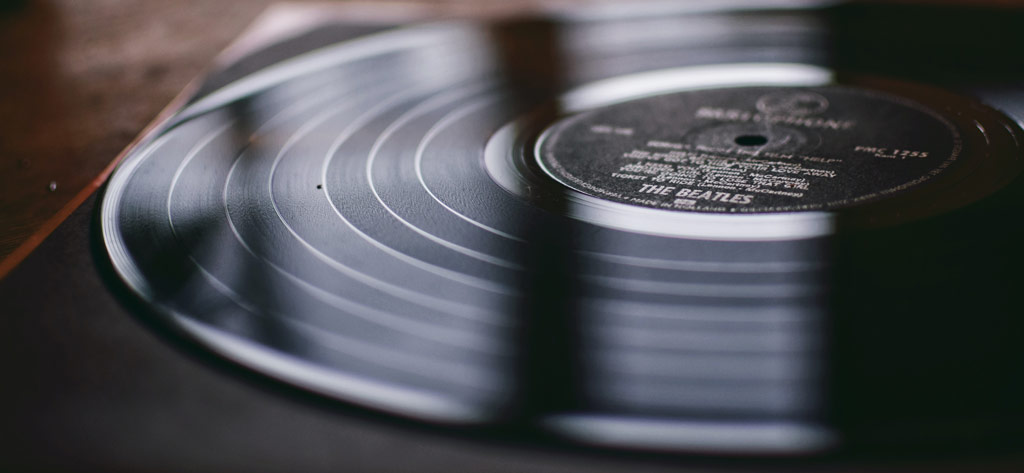
The Debut of Foam & Microfiber
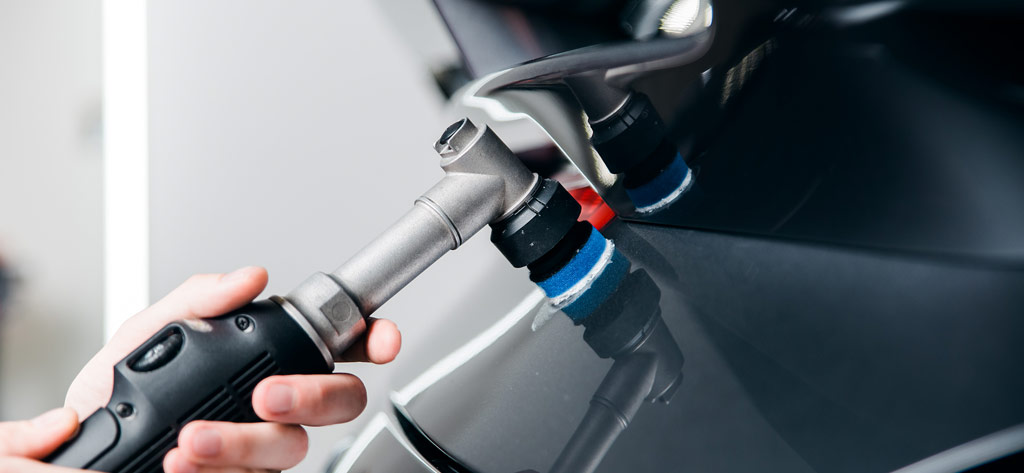
Partly in an effort to reduce this effect, manufacturers began developing foam pads. This innovative product offered a finer, uniform, and all around more consistent polishing pad texture. Softer foams in particular gave more control to the user, allowing them to abrade the paint surface less aggressively. This meant that a detailer could refine their polishing further, minimizing the appearance of leftover holograms as well as creating a higher ultimate level of gloss.
Alongside the introduction of foam pads, manufacturers created a new breed of polisher that did away with pure rotation, replacing it with an orbital action. With fixed or random options, this new kind of mechanical action completely eliminated the possibility of leaving behind holograms.
However, the downside of early orbital polishers was that they tended to have small throws of around 8mm traditionally. This made machine polishing safer and more accessible, which perhaps even kick-started the world of ‘hobby polishers’. Yet the gulf in cutting power between a small-throw orbital polisher with a foam pad and a rotary with a wool pad was enormous. For efficient, professional use, the small-throw orbital polisher was falling short.
Enter Buffer & Polisher Innovation
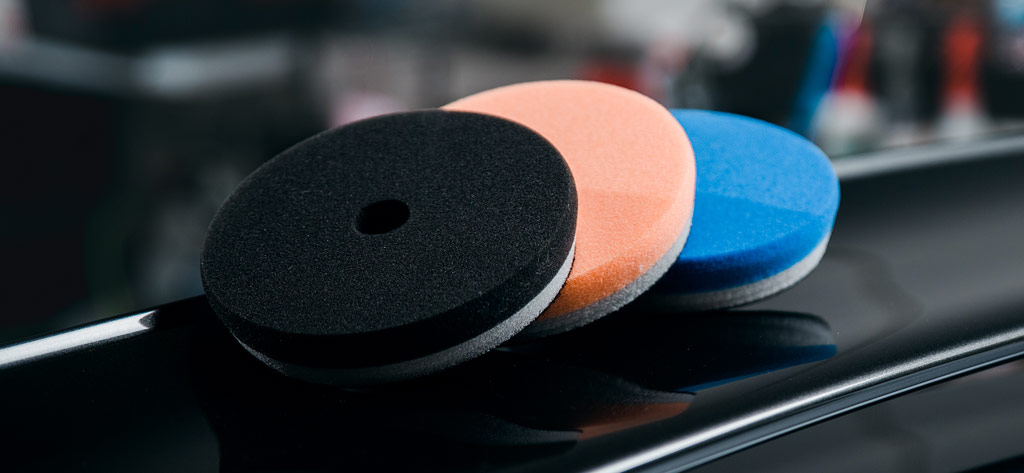
As a response to those aforementioned shortcomings, two big innovations occurred which have since taken the industry by storm over the last decade, creating a new ‘industry standard’ in many parts of the world. These breakthroughs are the large-throw orbital polisher, and the microfiber pad.
Both of these developments have given orbital polishers the power to compete with wool pads for ultimate cutting efficiency. The larger-throw orbital action means the tool is carrying out its correction work at a faster rate.
Combining that feature with a microfiber pad’s modern, synthetic take on the high compound-carriage and fiber abrasion characteristics of wool brings us to a place where we can enjoy all the benefits of an orbital polisher, devoid of a big drop in cutting performance; a stark contrast to the ‘old-fashioned’ rotary and wool pad combination.
One Person's "Old-Fashioned" is Another's "Classic"
Bob Seger once famously sang a tune that proclaimed his love for “that old time rock’n’roll,” and to many who work in automotive detailing, Seger’s sentiment resonates in their buffing pad preference. We are creatures of habit, and there will be a time when you find your groove and stick with it, for no reason other than the simple fact that it just suits your style.
Truth be told, a wool pad on a rotary buffer is still the go-to for pro detailers who need ultimate cutting, and because of all the aforementioned innovations available today, wool pads are vastly more effective, durable, and consistent than ever before.
This is why even our own Kelly Harris combines a wool pad with a rotary when he needs to remove severe defects, or tackle really hard or ceramic paint. Additionally, there are some circumstances where only a wool buffing pad will do the job, like in marine applications where a detailer battles a gelcoat.
When the going gets tough, no other types of buffing pad can quite match the wool pads of today. Don’t forget to check out the latest Lake Country Wool Pads available to you through your local supplier!